The art of plastics recycling is probably the last thing on the minds of the thousands who annually trudge New Zealand’s breathtakingly beautiful Tongariro track. But beneath their feet is bit of smart product design that reduces their environmental impact while also cutting the country’s industrial waste.
It’s called JakMatEnviro – honeycomb matting that helps stabilise and reduce the maintenance cost of wilderness tracks. Designed locally and made from locally recycled plastic, it’s good example of the Kiwi DIY gene in action.
“About three years ago, our accountant did the Tongariro Crossing. At that point, DOC was using geocell-type product imported from Germany. We thought we could do it better,” explains Jakaar Industries director Alan Holt. So they did.
Working closely with DOC, the company came up with design that provided greater flexibility, improved drainage, was easier to stack and carry and locked in place more firmly. It’s now being used in range of different wilderness environments – cutting both track maintenance costs and carbon emissions (including import costs and the helicopter time that goes into track maintenance).
Now the concept has been extended with ground stabilising geocell mat designed for carpark and utility area construction.
“It’s made from harder compound so it can take the weight of vehicles – there’s cost advantage but the appeal of the product is that you can get more environmentally sympathetic landscapes,” explains Jakaar’s market development manager John Bradley. “Well over 90 percent of the area of this product is available for grass growing.”
That’s not only more aesthetically pleasing but in more urbanised environments (stadiums, city parks) it also helps reduce stormwater run-off from parking areas – and helps protect grass over the wetter winter months.
Bradley, whose background includes focus on plastics recycling, is strong advocate for the born-again potential of the material.
“I’m great believer in the ability for plastic to have second life – if five percent of the characteristics are taken out from using it once, that would be large. There’s plenty more to be used again, to do another job. I would really encourage people to think about the ability to use recycled as percentage of their product because we know we can get it back to almost virgin state. So we can substitute anything from 10 percent to 100 percent.”
Prior to creating its geocell products, the Manukau-based, family-owned plastics engineering company was already on its own sustainability track. As well as maintaining fully certified ISO 9001 Quality System combined with the ‘TIMS’ integrated manufacturing system, it’s recently invested in the latest European electric moulding to cut its use of consumables (power, water, oil).
Its belief that plastic can be kept out of the waste stream is proved in its own operations – the waste from its range of injection moulded products all gets recycled on site and an increasing proportion of the company’s output (around 40 percent) is now made from recycled material.
“This [geocell] project is an especially good one for us,” says Holt. “We’re also making marker poles for tracks out of recycled material and we’re trying to push more product in that area.”
The company already has its eye on markets for both geocell products in Australia but is taking steady relationship-based approach to expansion.
“It’s about building relations, understanding the processes involved in laying it in different environments and building good dossiers of case studies for people to follow,” says Bradley.
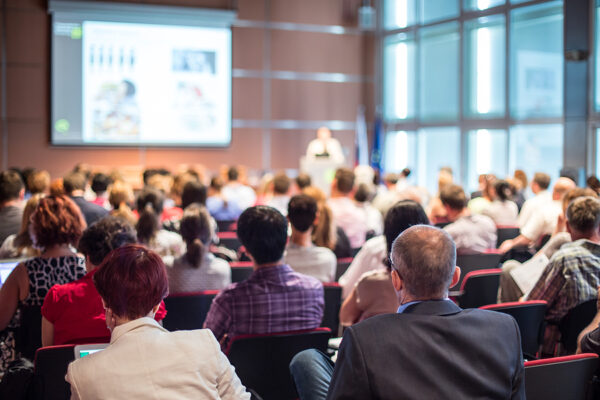
Forming partnerships with Māori business
Broadcaster and journalist Mike McRoberts (Ngāti Kahungunu) will be speaking to directors and the business community at an Institute of Directors’ event Te Ōhanga Māori: Connecting with the Māori economy.